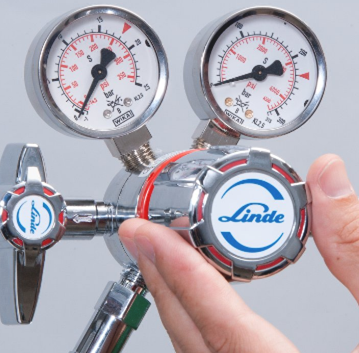
Flow Control Valves
In most air and hydraulic fluid power circuits, valves are used to control the direction, rate, and pressure in fluid lines. There are many different types of valves that can be used to achieve this control, and each valve has its own specific purpose.
Some valves can regulate flow while still allowing it to pass through another section while other types are designed to simply allow the flow to pass, stop, or switch direction.
Your traditional flow control valve will have a changeable aperture that can close to slow down the flow rate or open to increase the flow rate.
A flow control valve offers increased functionality in comparison to a traditional control valve, and they can allow you to regulate the pressure and flow.
What Are Flow Control Valves?
A flow control valves main purpose in pneumatics is to regulate the pressure or flow of a fluid. As a part of a pneumatic circuit, a flow control valves function is to reduce the rate of flow in a specific section, which then results in a slower actuator speed.
It’s designed so that the air will flow in one direction, which in turn, allows free flow in the opposite direction.
Some flow control valves can run backwards if there is a check valve bypass backwards.
There are different types of flow control valves, however, and they all serve a different purpose depending on what it’s machine is intended to do.
How Do Flow Control Valves Work?
Flow is directly proportional to speed and pressure is directly proportional to strength. If you increase the flow into an actuator, you will increase its speed. If you increase the pressure available to it, you are going to increase the strength available to it.
The flow changes the speed of an actuator, pressure changes the force of an actuator, and the valve position changes the direction of an actuator.
Flow control valves work by requiring a pressure differential between the upstream and downstream.
A flow control valve is connected to control the exiting pressure from the exhaust. This cause the air pressure to expel through a connection hose at a reduced rate.
So therefore, it’s not directly going to exhaust it and it has to travel through the valve at an increased resistance. It’s expelled extremely slowly, but is also proportionally controlled by the flow control valve.
If you adjust a flow control valve, you will notice that it will control the exiting exhaust rate and the extracting speed of the bore will be controlled.
The air traveling through is normally going to be put through the exhaust, in the case of using a flow control valve, it forces the air to be put through a path of resistance. Air is only allowed to travel in one direction directly through at full pressure.
When the air pressures traveling in the opposite direction through a path of increased resistance, it gets controlled proportionally by a valve control. This reduces the amount of exhaust that is being expelled.
Different Types of Flow Control Valves
As mentioned before, there are different types of flow control valves which all have different purposes. Depending on if the rate of flow needs to be regulated, accelerated, decreased, or altered in some shape or form, a differed type of control valve is going to be required.
Let’s take a look at some of the different types of flow control valves.
Traditional Control Valves
Control valves are valves used to control conditions such as flow, pressure, temperature, and liquid level by fully or partially opening or closing. Traditional control valves are the most basic type, and the flow control of a traditional control valve is limited to “fully open”, “fully closed”, or “fully switched” to a new flow path.
Traditional control valves are of simple design and capabilities. Changing direction, flow, or pressure during machine operation would require a complex hydraulic circuit.
Each desired direction, flow, or pressure would need an individual traditional valve to control it. Directional control valves would be a step up from a traditional control valve and they allow fluid into different paths from one or more sources.
They can control the stop, start, and change in the direction of flow of a pressure medium.
Needle Control Valves
A needle control valve is a variable control valve that is not pressure compensated. The fluid will come in and be forced to make two ninety degree turns and there is a needle in the valve in the way of the fluid.
It basically creates a pressure differential in between the upstream and the downstream. By varying how much that needle is in or out of the path of flow, you can change the flow rate coming through there by controlling the size of the orifice to allow more or less substance through.
One of the biggest shortcomings of the needle valve is that it restricts the flow rate in both directions. When you use a needle valve for speed control of a piston of an air cylinder in forward motion, it will also restrict motion in return stroke.
Ball Valves
These types of flow control valves have a perforated, hollow, and pivoting ball that is used to control the flow. It opens up when the hole of the ball lines up with the flow and closes when it becomes pivoted 90-degrees by way of the valve handle.
These types of flow control valves are very reliable and durable, even after going through many cycles.
Butterfly Valves
Butterfly Valves are used for the purpose of either regulating or isolating flow. It has a similar principle of operation to a ball valve, in the sense that it’s designed for a quick shut-off if necessary.
There is a disk located in the center of the pipe and a rod connected to an actuator which is passed through the disk. With butterfly valves, the disk is always present within the flow.
This means that a pressure drop is always induced in flow, irrespective of the positioning of the valve.
Globe Valve
This type of valve is designed to regulate flow in a pipeline. It has a stationary ring seat and has a disk-type element which is known as a plug.
The name is derived from its formerly typical spherical body shape and it has two halves of the body which are separated by an internal baffle. They are commonly used is plumbing and can be used to top flow.
These types of valves are used for applications that require frequent operation and throttling and are always reverse seated.